PRINCIPLES OF OPERATIONGENERAL DESCRIPTIONFig. 2 - In-Line Engine Model Description, Rotation and Accessory ArrangementFig. 3 6V Engine Model Description, Rotation and Accessory ArrangementFig. 4. Series 53 Cylinder ArrangementFig. 5 - Typical Model and Serial Numbers as Stamped on Cylinder Block (In-Line Engine)Cross Section Views of a Typical In-Line EngineCross Section Views of a Typical 6V-53 EngineENGINE SYSTEMSFig. 3 - Removing Injector from Cylinder HeadFig. 4 - Typical Fuel Strainer and Filter MountingFuel TankFig. 6 - Air Intake System Through Blower and Engine (In-line Engine)Fig. 9 - Heavy-Duty Oil Bath AirFig. 10 - Air Cleaner Tray (Plugged)Fig. 12 - United Specialties Dry Type Air CleanerCrankcase VentilationFig. 14 - Typical In-Line Engine Oil Filter MountingFig. 16 - Schematic Diagram of Typical In-Line Engine Lubricating SystemFig. 17 - Schematic Diagram of Typical 6V Engine Lubricating SystemFig. 18 Typical Cooling System for In-Line EnginesFig. 19 - Typical Cooling System for V-Type EngineENGINE COOLING SYSTEM MAINTENANCECooling System CleanersFig. 20. - Raw Water Pump Used on In-Line Engine.Raw Water PumpFig. 1 - Typical Instrument PanelThrottle ControlFig. 2 - Mechanical Shutdown System Schematically Illustrated.AUTOMATIC ELECTRICAL SHUTDOWN SYSTEMFig. 3. - Automatic Electrical Shut-Down System Diagram.Fig. 5 - Alarm System Wiring Diagram.ELECTRICAL STARTING SYSTEMHYDRAULIC STARTING SYSTEM (HYDROSTARTER)Fig. 7 - Hydrostarter Remote Control SystemLUBRICATION AND PREVENTIVE MAINTENANCECold Weather OperationFig. 8 - Typical Fluid Starting AidFig. 9 - Quick-Start AssemblyTRANSMISSIONS - POWER TAKE-OFF ASSEMBLIESFig. 11 - Checking Clutch Adjustment with a Torque Wrench and AdapterTORQMATIC CONVERTERSOPERATING INSTRUCTIONS - ENGINE OPERATING INSTRUCTIONSLubrication FittingsEngine TemperatureAvoid Unnecessary Engine IdlingFig. 1 - Location of Controls on Power Generator SetPREPARATION FOR STARTINGSTOPPINGLUBRICATION AND PREVENTIVE MAINTENANCEPreventative MaintenancePreventative Maintenance - ContinuedPreventative Maintenance - ContinuedPreventative Maintenance - ContinuedPreventative Maintenance - ContinuedPreventative Maintenance - ContinuedPreventative Maintenance - ContinuedPreventative Maintenance - ContinuedPreventative Maintenance - ContinuedPreventative Maintenance - ContinuedDETROIT DIESEL FUEL OIL SPECIFICATIONSDETROIT DIESEL FUEL OIL SPECIFICATIONSALTERNATE LUBRICANT SELECTIONSEMD OR RR OILSNEW ENGINE OIL CLASSIFICATION SYSTEMENGINE COOLANTFig. 2 - Heat Transfer CapacityFig. 3 - Coolant Inhibitor ChartGENERAL RECOMMENDATIONSGENERAL RECOMMENDATIONS - ContinuedENGINE TUNE-UP PROCEDURESEXHAUST VALVE CLEARANCE ADJUSTMENTFig. 2 - Adjusting Valve Clearance (Four-Valve Cylinder Head)Fig. 3 - Timing Fuel InjectorLIMITING SPEED MECHANICAL GOVERNOR AND INJECTOR RACK CONTROL ADJUSTMENTFig. 3 - Checking Rotating Movement of Injector Control RackFig. 5 - Adjusting Maximum No-Load Engine Speed (Type A)Adjust Maximum No-Load Engine SpeedFig. 8 - Adjusting Buffer ScrewLIMITING SPEED MECHANICAL GOVERNOR AND INJECTOR RACK - CONTROL ADJUSTMENTFig. 3 - Positioning No. 3L Injector Rack Control LeverFig. 5 - Checking Injector Control Rack SpringFig. 6 - Adjusting Maximum No-Load Engine SpeedAdjust Idle SpeedFig. 1 - Variable Speed Open Linkage Governor Mounted on EngineFig. 3 - Adjusting Injector Rack Control Lever Adjusting ScrewsFig. 5 - Adjusting Maximum No-Load Engine SpeedFig. 7 - Adjusting Buffer ScrewFig. 1 - Checking Governor GapFig. 3 - Checking Rotating Movement of Injector Control RackFig. 5 - Locating of Shims and StopsFig. 6 Adjusting Idle SpeedFig. 8 - Adjusting Booster SpringFig. 1 - Variable Speed Governor MountingFig. 3 - Positioning No. 3L Injector Rack Control LeverFig. 6 - Location of Shims and StopsFig. 7 - Adjusting Idle SpeedFig. 9 - Adjusting Booster SpringFig. 1 - Engine Load Limit DeviceFig. 3 - Throttle Delay Yield Lever (In-Line Engine)Fig. 5 - Adjusting Throttle Delay CylinderFig. 6 - Typical Speed Governor Lever PositionHYDRAULIC GOVERNOR AND INJECTOR RACK CONTROL ADJUSTMENTFig. 3 - Adjusting Length of Fuel RodFigure 5 - Adjusting Maximum Engine SpeedFig. 1 - Hydraulic Governor MountingPREPARING ENGINE FOR STORAGETORQMATIC CONVERTERPROCEDURE FOR RESTORING AN ENGINE TO SERVICE WHICH HAS BEEN IN EXTENDED STORAGEPOWER TAKE-OFFBuilt-in Parts BookBuilt-in Parts Book - ContinuedBuilt-in Parts Book - ContinuedBuilt-in Parts Book - ContinuedBuilt-in Parts Book - ContinuedBuilt-in Parts Book - ContinuedCYLINDER HEADCONNECTING ROD, PISTON AND LINEARACCESSORY DRIVE FOR BELT DRIVEN ACCESSORY (DRIVE HUB TYPE)INJECTOR AND CONTROLSAIR SHUT-DOWN HOUSINGBLOWER ASSEMBLY AND DRIVE (4 CYL)BLOWER ASSEMBLY AND DRIVE (6 CYL)OIL PUMP AND REGULATOROIL COOLEROIL COOLER (6V-53)FRESH WATER PUMPFAN MOUNT (6V-53)HEAT EXCHANGERWATER TEMPERATURE SHUTDOWN SWITCHTACHOMETER DRIVE COVERS AND ADAPTORSAIR COMPRESSOR AND DRIVEOWNER ASSISTANCEOWNER ASSISTANCE - ContinuedALPHABETICAL INDEXALPHABETICAL INDEX - ContinuedPART II. PARTS LISTING FOR DETROITTABLE OF CONTENTSDETROIT DIESAL ENGINE MODEL 353CYLINDER BLOCK (GROUP NO. 1.1000)CYLINDER BLOCK (GROUP NO. 1.1000) - ContinuedAIR BOX DRAINS (GROUP 1.1000A)CYLINDER HEAD (GROUP NO. 1.2000)CYLINDER HEAD (GROUP NO. 1.2000) - ContinuedENGINE LIFTER BRACKET (GROUP NO. 1.2000A)CRANKSHAFTCRANKSHAFT - ContinuedCRANKSHAFT FRONT COVER (GROUP NO. 1.3000A)CRANKSHAFT FRONT COVER (GROUP NO. 1.3000A) - ContinuedFLYWHEEL HOUSING (SAE #3)FLYWHEEL HOUSING (SAE #3)CONNECTING ROD & PISTONCAMSHAFT & GEAR TRAINCAMSHAFT & GEAR TRAIN - ContinuedACCESSORY DRIVE (HYDRAULIC PUMP)VALVE OPERATING MECHANISMVALVE OPERATING MECHANISM - ContinuedROCKER COVERFUEL INJECTOR (N-45)FUEL PUMPFUEL FILTERFUEL FILTER - ContinuedFUEL MANIFOLD CONNECTIONSFUEL MANIFOLD CONNECTIONS - ContinuedGOVERNOR HYDRAULICGOVERNOR HYDRAULIC - ContinuedGOVERNOR HYDRAULIC - ContinuedINJECTOR CONTROLSAIR CLEANER ADAPTORAIR INLET HOUSINGAIR INLET HOUSING - ContinuedBLOWERBLOWER - ContinuedOIL PUMPOIL PUMP - ContinuedOIL DISTRIBUTION SYSTEMOIL FILTEROIL FILTER - ContinuedOIL COOLERDIPSTICKOIL PANFRESH WATER PUMPWATER OUTLET ELBOWWATER OUTLET ELBOW - ContinuedRADIATORWATER CONNECTIONSFANEXHAUST MANIFOLDEXHAUST MANIFOLD - ContinuedSTARTING MOTORENGINE MOUNTTABLE OF CONTENTSTABLE OF CONTENTS - ContinuedSECTION II. GENERAL INFORMATIONIdentification Of Paver ComponentsFigure 6 - Correct Lifting Points (Four)MODEL BSF-400 ASPHALT PAVER DIMENSIONSFigure 9. Material Flow DiagramFigure 1. Instrument Panel - (Protective Cover In Unlocked Position)Figure 2. Diesel Engine - Left SideFigure 4. Travel & Conveyor Drive ArrangementsFigure 5. Friction Clutch- Main DriveFigure 7. 24 Speed Transmission-Manual ShiftsFigure 8. 24-Speed Transmission Selection PlateFigure 11. Location Of Clutch For RH TrackFigure 1. 12 VDC & 120 VAC Generators Detroit Diesel EngineFigure 3. 12 Volt Battery Location - LH Walkway RemovedMAIN ELECTRIC PANEL COMPONENTSAdjustment Of Brake Release CurrentTop View of Screed Junction BoxATTACHMENT OF A.C. TAP TO D.C. GENERATORELECTRICAL TROUBLESHOOTINGTROUBLESHOOTING THROTTLE CIRCUITTROUBLESHOOTING FEED CIRCUITTROUBLESHOOTING HYDRAULIC SOLENOIDSTROUBLESHOOTING VIBRATOR CIRCUITOperator's ConsoleTROUBLESHOOTING VIBRATOR CIRCUIT - ContinuedWiring DiagramSECTION V. Hydraulic SystemRepresentative Drawing of Hydraulic System ComponentsRH Sub-deck Area - (Walkway Removed)Figure 5 - Line Filter & Filter Condition GaugeFigure 7 - Paver Control ConsoleFigure 9 - Solenoid Valve - Cross SectionFigure 10 - 4 Way Solenoid Operated Hydraulic Valve - Exploded ViewPreparation For Dismantling Valve Bank Figure 12 - Exploded View Of Valve BankPressure Relief Valve Figure 15 - Pressure Relief Valve - Cross SectionTypical Hoper Wing Cylinder - Double Acting, Double Stage TypeFigure 19 - Tilting Hopper WingsFigure 22 - Hose AssemblyTROUBLE-SHOOTING GUIDE FOR BSF-400 PAVER HYDRAULIC SYSTEMSchematic Diagram-BSF-400 Paver Hydraulic SystemSECTION VI. Asphalt Spreading System (Feed)Slat Conveyors and Spreading Screws (Screed Removed)Screw Conveyor Extensions (Uncoupled)Recommended Setting Of Control AssembliesRange of Depth Feeler Switch LocationFloating Screed AssemblyMaking Mat Thickness Adjustment - R.H. SideHandwheels Set to Level Inclined RoadwayScreed Bottom with Crowning ArmsScreed Side Plate & Bevel Guide PlateMethod of Attaching Chain for BleedingCut-Off Shoe Installed on L.H. Side PlateEffect of Pull-point Height on Screed WearChecking Height of Flat Strike-offFlat Strike-off Adjusted Too LowASSEMBLY OF SCREED EXTENSIONINSTALLATION OF SCREED EXTENSIONINSTALLATION OF SCREED EXTENSION - ContinuedINSTALLATION OF SCREED EXTENSION - ContinuedCut-away Of Screed Showing Heating SystemRear View Of Screed And Burner AssemblyExploded View of Screed HeaterTop View of Screed Junction BoxFigure 38 Adjusting Screed Vibrator IntensityPaving with Operator in Right Hand Seat PositionAdjustable Material Depth Control Switch with Feeler Arm - R.H. Assembly ShownPRE-START CHECK (DAILY REQUIREMENT)Cleaning paver with Screed Heater Fuel Spray AccessoryMain Electrical PanelBURNISHING TRACK CLUTCH & BRAKE FACINGS TO IMPROVE PERFORMANCESECTION IX. PLANNING THE PAVING JOBUsing Guide Marker, Reference Line and Cut-off ShoeAdjusting Right Hand Hopper GateSelecting Proper Operating SpeedsEdges Loose - Decrease Front CrownEnding A MatMat ConditionsAPPLICATION OF ASPHALTIC MATERIALSMat Surface Before Adding Silicone CompoundSlope Conversion TableTROUBLE-SHOOTING CHARTSECTION X. CLEANING and LUBRICATING PAVERPlastic Lubricap for Bearing Grease FittingsLUBRICATION DETAILScreed Adjusting Mechanism and Pull ArmsASPHALT PAVER LUBRICATION CHARTASPHALT PAVER LUBRICATION CHARTTABLE OF CONTENTSTABLE OF CONTENTS - ContinuedCRAWLER TRACKSTrack Tension Adjustment (Factory assembly view)Crawler Track Drive Detail - R.H.REPLACEMENT OF TRACK DRIVE & CHAIN SPROCKETS WHICH WERE HUCK-BOLTED TO HUBCHECKING & ADJUSTING TRACK DRIVE TRANSFER CASESTRANSFER CASE INSPECTION & ADJUSTMENTL.H. Transfer Case (Current Model) - Cross Section View Figure 12Reading Rolling Torque Test Scale CASE REPAIRTransfer Case - Top View Slat Conveyor Chain Tightener (Four Used)Slat Conveyor Liner Detail Cross-section Thru Screw Flight & Liner ELECTRIC CLUTCHES - TRAVEL & FEEDCross-section Thru Electric Feed Clutch (Travel clutch identical except for hub)SCREED UNITHANDWHEEL SCREW MAINTENANCEHandwheel Coupling With Ball Bearing & One-piece Bearing HousingVIBRATOR CONTROL KNOB INSTALLATIONDetail Of Brake Auto-gap Drive PinMethod Of Measuring Wear Of Electric BrakeCOMPONENT PARTS IDENTIFICATION - TWIN DISC C-110 CLUTCHPower Take-off & Clutch Assembly for GM Diesel EngineCross-section View Of 24 Speed Manual Shift Transmission - (View A-A, Figure 52)COMPONENT PART DESCRIPTIONS - 24 SPEED TRANSMISSION (FIGURE 51)COMPONENT PART DESCRIPTIONS - 24 SPEED TRANSMISSION (FIGURE 52)Cross-section View of 24 Speed Manual shift Transmission (View C-C, Figure 51)Side & End View Cross-sections Of 6 Speed Shift Lever ModuleREPLACEMENT OF TRANSMISSION OIL PUMPTransmission Oiling system - Exploded ViewChecking Belt Tension Using Pencil Type GaugeCorrect Alignment of Generator PulleySEASONAL OVERHAULPART IV. VANE PUMPSTABLE OF CONTENTSPURPOSE OF MANUALTABLE II - MODEL CODE BREAKDOWNSection III - PRINCIPLES OF OPERATIONFLOW CONTROL AND RELIEF VALVESHAFT ROTATIONOPERATING TEMPERATURESection V - SERVICE, INSPECTION AND MAINTENANCETABLE IV - TROUBLE SHOOTING CHARTSection VI - OVERHAULFigure 7Section VII - TESTINGPart V. Service Instructions for Cyclopac Series Air CleanersBaffle AssemblyService ProcedureElement Cleaning MethodSECTION INDEXSECTION 1. COMPONENTSSECTION 1. COMPONENTS - ContinuedSection 2. TrackSection 2. Track - ContinuedTRACK SPRINGREAR SPROCKETTAKE-UP IDLERUPPER ROLLERLOWER ROLLERTRACK ROLLER PIVOT SHAFTMAIN FRAMEWALKING BEAMBEAM ROLLER ASSEMBLYGATEHOPPER WINGSCYLINDER-HOPPER WINGSTRACTOR ACCESSORIESTRACTOR ACCESSORIES - ContinuedHOODS, COVERS AND WALKWAYSACOUSTIC MATERIAL HOODS, COVERS, WALKWAYSOPERATORS SEAT STANDARDSLAT CONVEYORSLAT CONVEYORANTI-FRICTION BEARING - FLANGE TYPEANTI-FRICTION BEARINGS-Flange Type - ContinuedSLAT CONVEYOR CHAINSLAT CONVEYOR LINER ASSEMBLYGREASE PIPING - SLAT CONVEYORGREASE PIPING - SLAT CONVEYOR - ContinuedSKIRTBOARD AND COVERS - SLAT CONVEYORGREASE PIPING - SCREW CONVEYORSCREW CONVEYOR - 14" DIAMETERSCREW CONVEYOR - 14" DIAMETER - ContinuedREMOTE ADJUSTABLE SCREW CONTROLSCREED PULL ARMS - STANDARDSCREEDSCREED - ContinuedSCREED - ContinuedDUAL CROWN ADJUSTING MECHANISMSCREED ADJUSTING MECHANISMSCREED ADJUSTING MECHANISM - ContinuedBURNER AND OIL LINESCREED OIL BURNERSCREED OIL BURNER - ContinuedELECTRODE AND OIL PIPESCREED LIFTSCREED LIFT - ContinuedCYLINDER - SCREED LIFT12" SCREED EXTENSION - WITH ADJUSTABLE STRIKE - OFFS12" SCREED EXTENSION - WITH ADJUSTABLE STRIKE - OFFS - ContinuedSCREW EXTENSIONSHEAT DUCT EXTENSIONMATERIAL RETAINING PLATESMATERIAL RETAINING PLATES - ContinuedPOWER MOUNTING AND DRIVE COMPONENTSPOWER MOUNTING AND DRIVE COMPONENTSPOWER MOUNTING PARTSPOWER MOUNTING PARTSPOWER MOUNTING PARTS - ContinuedPOWER MOUNTING PARTS - ContinuedHYDRAULIC PUMPAIR CLEANER AND EXHAUST SYSTEMAIR CLEANERALTERNATOR AND DRIVEGENERATOR AND DRIVEOPERATING AND MAINTENANCE INSTRUCTIONSALTERNATORLOAD CONNECTIONSHEAVE & BELT ALIGNMENTLOW OUTPUT VOLTAGEStep by Step Check ListCheck for Defective DiodeBRUSHHOLDER ASSEMBLYTESTING A FIELD CIRCUITFIELD ASSEMBLY (Continued)STATOR ASSEMBLYPARTS LISTPARTS LIST - ContinuedWIRING DIAGRAMAUTOMATIC THROTTLE CONTROLAUTOMATIC THROTTLE CONTROL - ContinuedPOWER TAKE-OFF - DIESEL ENGINEPOWER TAKE-OFF - DIESEL ENGINE - ContinuedTWIN DISC CLUTCH24 SPEED TRANSMISSION, CLUTCH & DRIVE SHAFTCOUPLING AND SHEAVEELECTRIC CLUTCH - 12 VOLT24 SPEED TRANSMISSION24 SPEED TRANSMISSION - Continued24 SPEED TRANSMISSION - ContinuedRANGE SHIFTRANGE SHIFT - Continued6 SPEED SHIFTER6 SPEED SHIFTER - ContinuedFORWARD AND REVERSE SHIFTFORWARD AND REVERSE SHIFT - ContinuedSPICER UNIVERSAL JOINTCLUTCH, TRANSFER CASE AND BRAKESCLUTCH, TRANSFER CASE AND BRAKES - ContinuedTRANSFER CASETRANSFER CASE - ContinuedTRANSFER CASE - ContinuedELECTRICALLY RELEASED BRAKE - 12 VOLTELECTRIC CLUTCH - 12 VOLTSTANDARD CONVEYOR DRIVESSTANDARD CONVEYOR DRIVESANTI-FRICTION BEARING ASSEMBLIESANTI-FRICTION BEARING ASSEMBLIES - ContinuedHYDRAULIC COMPONENTSHYDRAULIC RESERVOIR, FILTER & RELIEF VALVEHYDRAULIC RESERVOIR, FILTER & RELIEF VALVE - ContinuedHYDRAULIC RELIEF VALVE ASSEMBLYHYDRAULIC LINES - HOPPER WINGSHYDRAULIC LINES - SCREED LIFTHYDRAULIC LINES - SCREED LIFT - ContinuedHYDRAULIC VALVE BANK4-WAY SOLENOID VALVEHOLDING VALVE - SCREED LIFTBASE ELECTRIC PARTSBASE ELECTRIC PARTS - ContinuedMETER BOX - MILITARY PAVER-VSF-400CONTROL CONSOLECONTROL CONSOLE - ContinuedCONTROL BOX PARTSCONTROL BOX PANELCONTROL BOX PANEL - ContinuedPAD, BRAKEELECTRICAL CABLESELECTRICAL CABLES - ContinuedELECTRICAL PARTS - SCREEDSCREED ELECTRICAL BOXPULSATORSCREED VIBRATORSCREED VIBRATOR - ContinuedTABLE OF CONTENTSTABLE OF CONTENTS (Continued)SECTION I. GENERALPersonnel and TrainingReportingSECTION II. MAINTENANCEShipment and StorageSECTION III. REPAIR PARTS SUPPLYRequisitioning Repair Parts .REFERENCESREFERENCES - ContinuedWARRANTY GUIDELINESWARRANTY GUIDELINES - ContinuedAPPENDIX C. MAINTENANCE ALIOCATION CHARTAPPENDIX C. MAINTENANCE ALIOCATION CHART - ContinuedSection II. MAINTENANCE: ALLOCATION CHARTSection II. MAINTENANCE: ALLOCATION CHART - ContinuedSection II. MAINTENANCE: ALLOCATION CHART - ContinuedSection II. MAINTENANCE: ALLOCATION CHART - ContinuedSection II. MAINTENANCE: ALLOCATION CHART - ContinuedSection II. MAINTENANCE: ALLOCATION CHART - ContinuedSection II. MAINTENANCE: ALLOCATION CHART - ContinuedSection II. MAINTENANCE: ALLOCATION CHART - ContinuedSection II. MAINTENANCE: ALLOCATION CHART - ContinuedSection II. MAINTENANCE: ALLOCATION CHART - ContinuedSECTION III - TOOL AND TEST EQUIPMENT REQUIREMENTSSECTION III - TOOL AND TEST EQUIPMENT REQUIREMENTS - ContinuedCCE MANUFACTURER FIELD CAMPAIGNS AND MODIFICATION PROCEDURESBASIC ISSUE ITEMS LISTITEMS TROOP INSTALLED OR AUTHORIZED LISTAPPENDIX G. INITIAL RECOMMENDATION - PRESCRIBED LOAD LIST (PLL) - AUTHORIZED STOCKAGE LIST (ASL)APPENDIX. SAMPLE FORMAT - DA FORM 2765 PART NUMBER REQUESTSAMPLE FORMAT - MILSTRIP REQUISITION FOR (NSN)SAMPLE FORMAT - MILSTRIP REQUISITION FOR (NON-NSN)SAMPLE FORMAT - MILSTRIP REQUISITION FOR (NON-NSN) - ContinuedSAMPLE FORMAT - MILSTRIP REQUISITION FOR (NON-NSN)(MANUAL)INSTRUCTIONSCROSS REFERENCE PART NUMBER LISTCROSS REFERENCE PART NUMBER LIST - ContinuedMAINTENANCE AND OPERATING SUPPLY LISTMAINTENANCE AND OPERATING SUPPLY LISTPREVENTIVE MAINTENANCE CHECKS AND SERVICESPREVENTIVE MAINTENANCE CHECKS AND SERVICES - ContinuedOPERATOR/CREW PREVENTIVE MAINTENANCE AND SERVICESOPERATOR/CREW PREVENTIVE MAINTENANCE AND SERVICES - ContinuedOPERATOR/CREW PREVENTIVE MAINTENANCE AND SERVICES - ContinuedOPERATOR/CREW PREVENTIVE MAINTENANCE AND SERVICES - ContinuedOPERATOR/CREW PREVENTIVE MAINTENANCE AND SERVICES - ContinuedOPERATOR/CREW PREVENTIVE MAINTENANCE AND SERVICES - ContinuedOPERATOR/CREW PREVENTIVE MAINTENANCE AND SERVICES - ContinuedCleaning and Lubricating PaverLUBRICATION - GENERAL SUGGESTIONSLubrication DetailLubrication Detail - ContinuedASPHALT PAVER LUBRICATION CHARTASPHALT PAVER LUBRICATION CHARTENGINE STANDARD AND OPTION EQUIPMENT
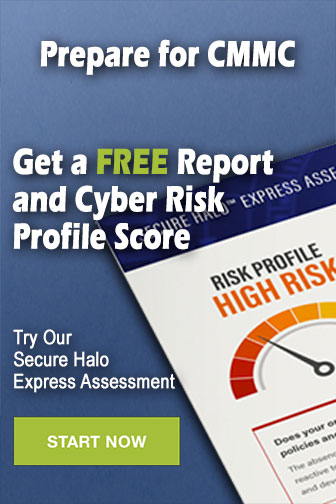