TM 5-3895-373-34
CHAPTER 2
DIRECT SUPPORT/GENERAL SUPPORT MAINTENANCE
OF PAVING MACHINE
2.1
GENERAL MAINTENANCE PROCEDURES.
General maintenance procedures include procedures to
follow for equipment washdown, component cleaning,
removal and disassembly, inspection, reassembly and
installation, and repainting. Refer to maintenance tasks
for specific guidelines. All maintenance operations must
include good shop practices and proper safety. Some
general maintenance procedures are as follows:
a.
Wear
protective
clothing
as
specified
in
maintenance tasks. Observe all warnings, cautions, and
notes specified in maintenance tasks.
b.
Areas of the paving machine exposed to paving
material require washdown prior to maintenance. Use
spray washdown equipment located on the paving
machine in an approved washdown area. Use
mechanical means such as scrapers and stiff wire
brushes to remove paving material buildup. Dispose of
paving material residue in accordance with local
hazardous material disposal procedures.
c.
Clean components before servicing. Steam
cleaning may be required. Use cleaning solvent as a
general degreaser unless specified otherwise in the
maintenance task. Rinse all components thoroughly with
cleaning solvent. Use a stiff bristle brush to remove
hardened deposits.
d.
Unless otherwise specified in maintenance
procedures, all fasteners are treated with thread locking
compound. If the fastener cannot be removed by
mechanical methods, heat fasteners with heater gun to
500° to 600°F (2320 to 315°C) for several minutes. Use
thread locking compound solvent to remove thread
locking compound from fasteners after they are removed
from the machine. If thread locking compound solvent
does not remove buildup on threads, discard fastener.
e. Use a backup wrench when loosening or
tightening inline fittings. Using a backup wrench will
prevent unnecessary damage to attached lines and/or
smaller fittings.
f. During removal and disassembly procedures,
inspect all parts and components for signs of wear or
damage. Discard all gaskets and preformed packings.
When scraping gasket material from parts, do not
scratch or gouge metal surfaces. Check for cracked or
warped castings. Clean all parts with cleaning solvent
after
inspection
unless
specified
otherwise
in
maintenance task. Dry parts with a clean, cleaning cloth
or compressed air. For critical internal hydraulic
components, use a clean, lint-free cloth. Do not use
greater than 30 psi (207 kPa) maximum air pressure to
dry components. Protect internal parts of engine and
hydraulic components to prevent contamination after
cleaning. Always tag electrical wires, harnesses,
hydraulic hoses, fuel hoses, coolant hoses and metal
tube assemblies, etc, prior to removal. Cap or plug
hydraulic and fuel hoses and fitting after removal.
g. During removal and disassembly procedures,
check all fasteners for damaged threads. Replace
damaged fasteners. Drill out any broken bolts or studs.
Retap holes to correct size after drilling. Replace all
lockwashers and self-locking nuts. Replace distorted flat
washers.
h. Observe all torque values stated in maintenance
tasks. Torque values are based on modified SAE Grade
8 fasteners and clamping load.
i. Replace all tie-wraps removed from hoses and
wiring. Replace tie-wrap in approximately the same
positions they were in prior to removal.
j. Check hydraulic hoses for leaks, blisters, or
kinks. Replace damaged hydraulic hoses. Check
hydraulic fittings for damage or stripped threads.
Replace fittings if damaged. Use protective caps and
plugs on lines and components to prevent contamination.
Use only clean hydraulic oil when refilling hydraulic
systems. Lubricate all seals and preformed packings
when reassembling hydraulic components. Replace
missing, worn, or damaged chafing gear.
2-1
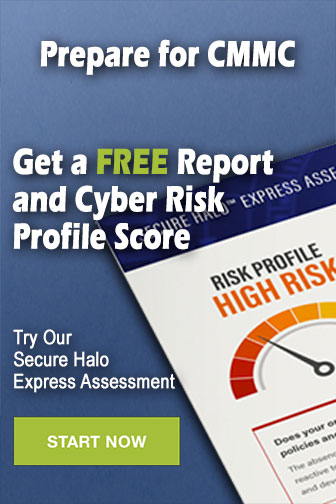